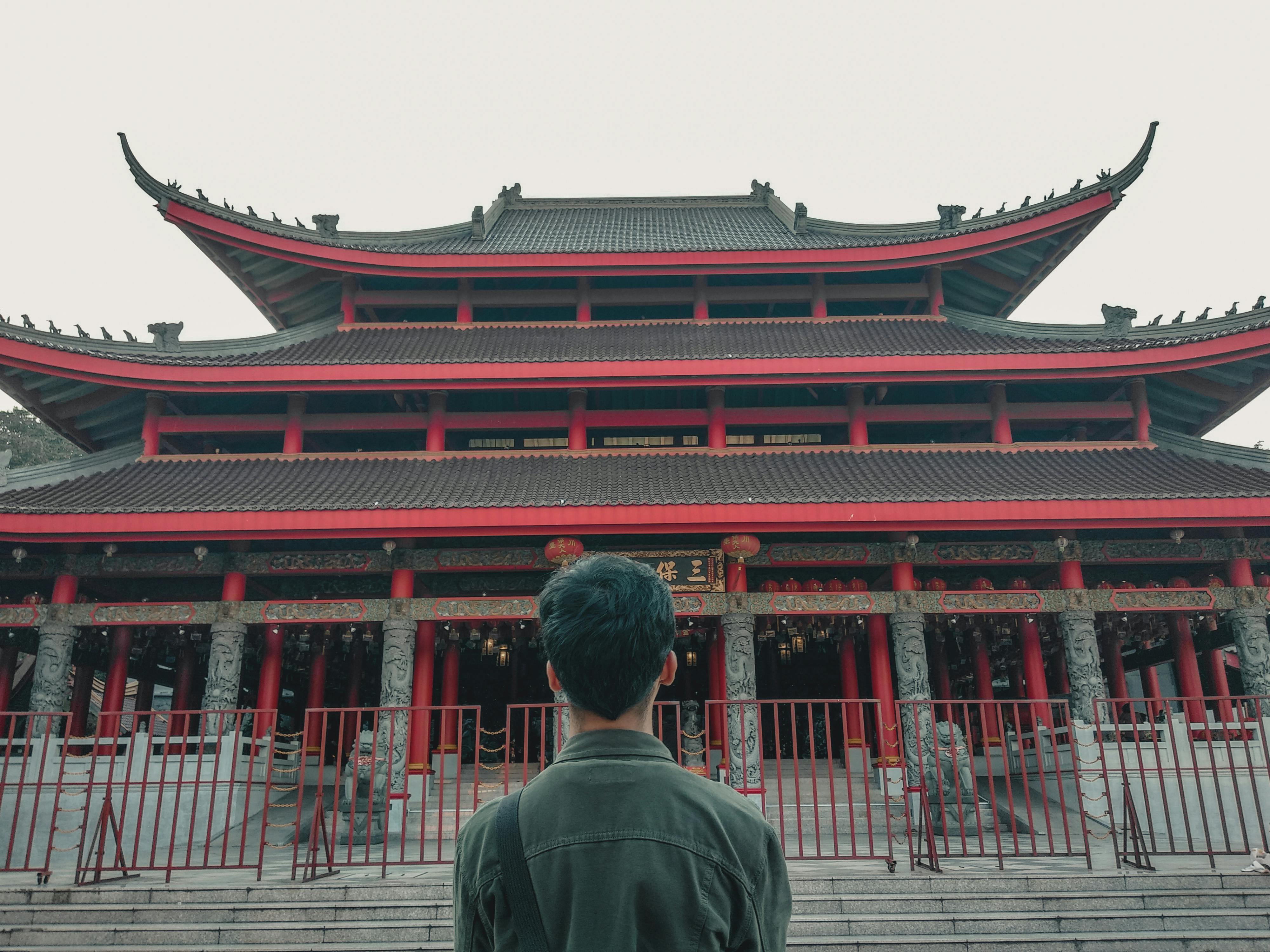
Manufacturers of electronic devices, from home audio equipment to automotive keyless entry systems, are increasingly looking for a reliable and cost-effective method to uniquely identify and track products through the manufacturing cycle, sales distribution and verification of the guarantee after the sale. An automated, stand-alone tracking system requires a permanent machine-readable code to be applied to an internal printed circuit board to uniquely identify each product. The code must be durable enough to survive manufacturing processes including wave soldering and board cleaning, must not affect circuit performance, and must store information in the small space available on mindful PCBs. of real estate.
2D matrix code provides a means of storing strings of alphanumeric characters in very small areas of the printed circuit board. Laser marking technology provides a method to permanently apply 2D matrix codes to most plate substrates. The high resolution and high accuracy of beam-directed laser marking systems provide the means to create highly reliable, well-defined codes, regardless of code size. Laser marking also provides the user with a computer controlled marking process for easy implementation in automated product tracking systems.
2D ECC 200 Matrix Codes
Two-dimensional symbologies encode information in the form of a checkerboard pattern of on/off cells. Specific advantages of Data Matrix codes over conventional 1D barcodes include:
· Encodes information digitally, as opposed to analog encoding of data in conventional barcodes.
Can accommodate low-contrast printing directly on parts without the need for a label
Offer a very high information density, the highest among other common 2D codes, which means you can fit a lot of information in a very small area.
· They are scalable, meaning you can print and read them at various magnification levels, limited only by the resolution of available printing and imaging techniques.
Due to the high information density inherent in Data Matrix codes, they also offer built-in error correction techniques that allow the full recovery of the encoded message in a Data Matrix symbol even if the mark is corrupted and up to 20% missing Of code. symbol.
· They are read by video cameras instead of a scanning laser beam used to read conventional barcodes, which means they can be read in any orientation.
ECC 200 Data Matrix is the most popular 2-D symbology with wide use in automotive, aerospace, electronics, semiconductors, medical devices, and other traceability applications at the manufacturing unit level. Data Matrix codes do not typically replace conventional linear barcodes, but are used when traditional barcodes were too large, did not provide enough storage capacity, or were unreadable.
Data matrix code structure
2D matrix codes appear as a “checkerboard” with the individual squares (cells) in an on (white) or off (black) state. The code consists of four distinct elements.
The Finder “L” pattern consists of a solid row of cells along the left edge and bottom of the code that guides the reader into the 2D code layout.
· The clock track is a sequence of on/off cells along the right edge and top of the code that designates the row/column count for the reader.
The data region is the pattern of black and white cells within the L pattern and the clock tracks that contain the alphanumeric content of the code.
The quiet zone around the code should be free of features that might be visible to the reader. The quiet zone must be at least two rows/columns wide for codes built with square cells. The quiet zone must be at least four rows/columns wide for codes built with circular cells (dots).
ECC 200 Data Matrix codes can store up to 3,116 numeric, 2,335 alphanumeric, or 1,555 bytes of binary information in a 144 column by 144 row matrix. The dimensions of the most realistic symbols for printed circuit boards can still contain a significant amount of information.
laser marking system
The laser marking system consists of the laser source, beam shaping optics, and beam steering system.
The laser is a light amplifier that generates a bright, collimated beam of light at a specific wavelength. For FR4 and welding mask applications, most users choose the air-cooled CO2 laser that operates in the far-infrared wavelength of 10,640nm. This laser offers several performance and cost advantages and produces excellent marking results.
The laser beam is projected through two beam deflecting mirrors mounted on high-precision, high-speed galvanometers. As the mirrors rotate under the direction of the system’s computer, the laser beam scans the target’s marking surface to “draw” the desired marking image.
After the laser beam is deflected from the beam steering mirrors, it is focused to the smallest possible spot using flat field focusing optics. The Flat Field Focus Assembly is a multi-element optical device designed to keep the focal plane of the focused laser beam in a relatively flat plane throughout the marking field. Focused laser light significantly increases power density and associated marking power.
The function of the laser optical train is to focus the laser beam on a small spot and scan the laser beam on the target surface with high speed and precision. With the CO2 laser configuration, the diameter of the focused spot and the width of the associated marking line is approximately 0.0035″ to 0.004″. Human readable text characters can be as small as 0.040″ and 2D matrix codes can be built from individual features as small as a single 0.004″ dot.
PCB marking
For marking printed circuit boards, the heat generated by the laser beam thermally alters the surface of the board to create a contrasting, legible mark. The process does not require labels, stencils, punches or any other auxiliary or consumable hardware.
For printed circuit board applications, several different variations of this technique can be used for different board/cladding materials and background conditions.
Soldermask or other conformal coatings on FR4 plates –
The laser beam can alter the texture of the coating, giving it a lighter contrasting appearance, or it can completely remove the coating to expose the underlying substrate or copper ground plane.
FR4 uncoated –
The laser beam alters the surface texture of the FR4 producing an almost white appearance.
Screen printed ink block –
For users who have already screen-printed component identification or other fixed information on cards, a screen-printed white ink block can serve as the background for the 2D matrix code to optimize readability. This technique is particularly useful when…
o The background color of the whiteboard is similar to the color of the laser mark.
o The underlying circuitry would hide the marking image from code readers.
o The plate material is not suitable for laser marking, such as ceramic substrates.
2D matrix code verification
Checking the readability and content of the 2D matrix codes is an important step in the overall quality program. After each circuit is marked, the reader verifies the integrity of the mark before indexing the laser marking head to the next marking location. The reader retrieves the alphanumeric text string from the 2D code and compares it to the text string to be marked.
The reader also evaluates code readability based on a variety of parameters including foreground/background contrast, geometric accuracy (skew, squareness, etc.), and dimensional accuracy of marked and unmarked cells. The 2D matrix codes are then classified as pass (green), warn (yellow), or fail (red). For overall production efficiency, the laser system can be programmed to check only a select few 2D codes on a panel, then automatically switch to check each code if the code readability falls below a specified level.
Today’s scanners do an excellent job of reading low-contrast 2D codes. If the laser marking system is installed on an assembly line with older 2D array readers downstream of the laser marker, the verification reader can be configured to evaluate codes based on the performance of older readers to ensure consistent performance throughout the assembly process.
MarkedPerformance
The typical PCB marker is a SMEMA compliant, fully automated through-conveyor laser marking system. Overall laser marker productivity is made up of several steps that make up the marking cycle. The steps required to mark a multi-array panel are…
1. Transport and positioning of the panel in the marking area.
2. Trust location detection (optional)
3. Marking of the first circuit of the matrix.
4. Verification of the marked 2D matrix code (optional)
5. Movement of the laser marking head to the next circuit in the array.
6. Repeat steps 3 and 4 for the remaining circuits in the array.
7. Transport of the panel outside the laser marking system (synonymous with bringing the next panel)
Cost of operation
The cost of operation is much less than $1.00 per hour. Typical utility requirements are 110VAC, single phase, 12A. A source of compressed air is required for pneumatics. Total utility costs at full laser power (laser should operate at less than 80% of rated power) is $0.12 per hour. The main consumable item is the CO2 laser tube which needs to be replaced every 3 to 5 years at a typical cost of $1,000.00 to $1,500.00. Assuming a 40-hour work week and a 3-year tube life, the tube replacement cost would equal $0.18 per hour for a total operating cost of $0.30 per hour under worst case conditions. Actual operating costs will be lower due to less than maximum electrical usage and longer tube life.
For typical pcb laser marking applications, the cost of marking is less than $0.0003 per circuit.
Resume
The electronics industry has been searching for a cost-effective and technically effective means of applying machine-readable codes to printed circuit boards since the 1980s. Early attempts included laser marking linear barcodes on the edge of the board, a daunting challenge for reader alignment, and marking linear barcodes next to circuit traces also a challenge for barcode readers. Barcode content was limited to a few characters due to the limited space and character per inch capacity of barcodes.
The development of 2D matrix code combined with the resolution, permanence, and speed of beam-directed laser marking technology now offers manufacturers a reliable, cost-effective, flexible, and verifiable means of uniquely identifying each product through production. , distribution and post-sale.